The Kegonsa Anagama Kiln
Anagama kilns were developed in China and were used extensively in 16th-17th century Japan for the production of tea ceremony objects. These kilns required extended firings to reach temperatures sufficient to harden or vitrify many of the clays that were being used. Initially, the potter’s intention was to vitrify the clay and produce more durable wares. Through time it became apparent to these early artisans that the natural glazing of the pieces, as a result of this wood-fire process, offered a beautiful aesthetic of its own.
When high temperature (vitrification) is achieved (2200-2450 F), wood ash combines with the clay to produce a natural glaze. Careful placement of the pieces in the kiln directs the flame and ash producing a wide range of patterns, textures, and colors of the natural glaze. The range of glaze effects on each piece is determined by the firing technique, composition of the clay, temperature, proximity to the burning wood, and placement in relation to other pieces.

The Kegonsa Anagama is 20 feet in length and was designed to maximize the front firebox area in which burning embers are in direct contact with many of the ceramic pieces (about 1/3 of the total stacking). Firings typically last 6-8days. Pieces throughout the kiln collect a significant amount of fly ash as a result of the wide front, low arch, tapered back, and minimal slope from front to back (slope is less than 10 degrees). The kiln’s tapered back also lends itself to a more reduced atmosphere and increased flame velocity which creates varied surfaces that compliment those commonly produced in the firebox. In addition to the “action” of the fire many pieces in the Kegonsa Anagama are glazed prior to firing. This approach reflects an interest in a non-traditional approach to anagama wood-firing and serves to broaden the palette of the natural ash glaze.
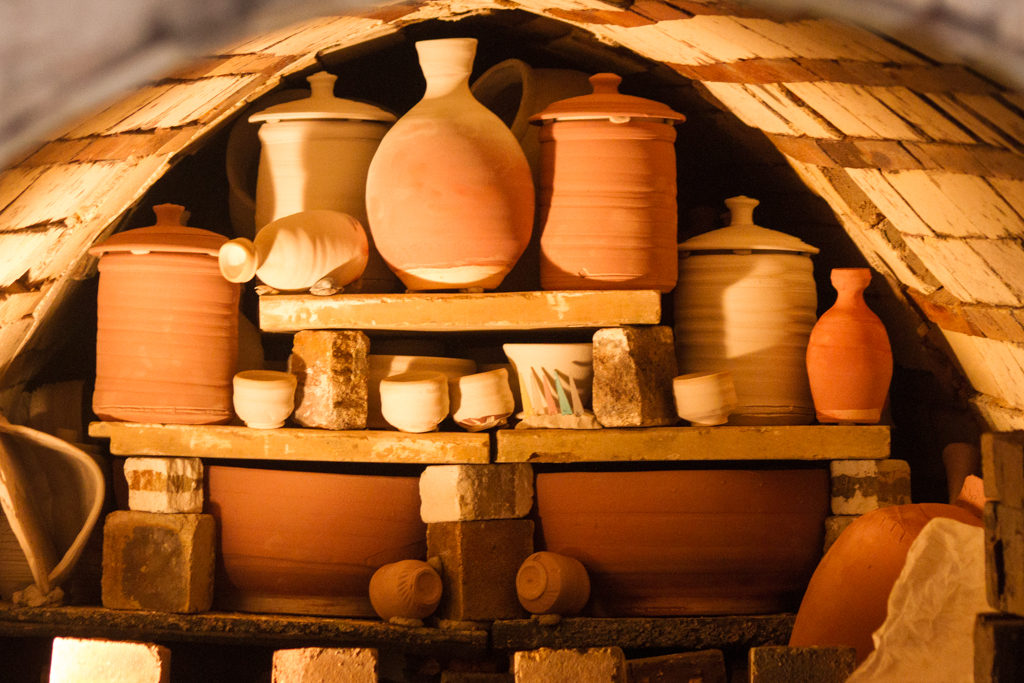


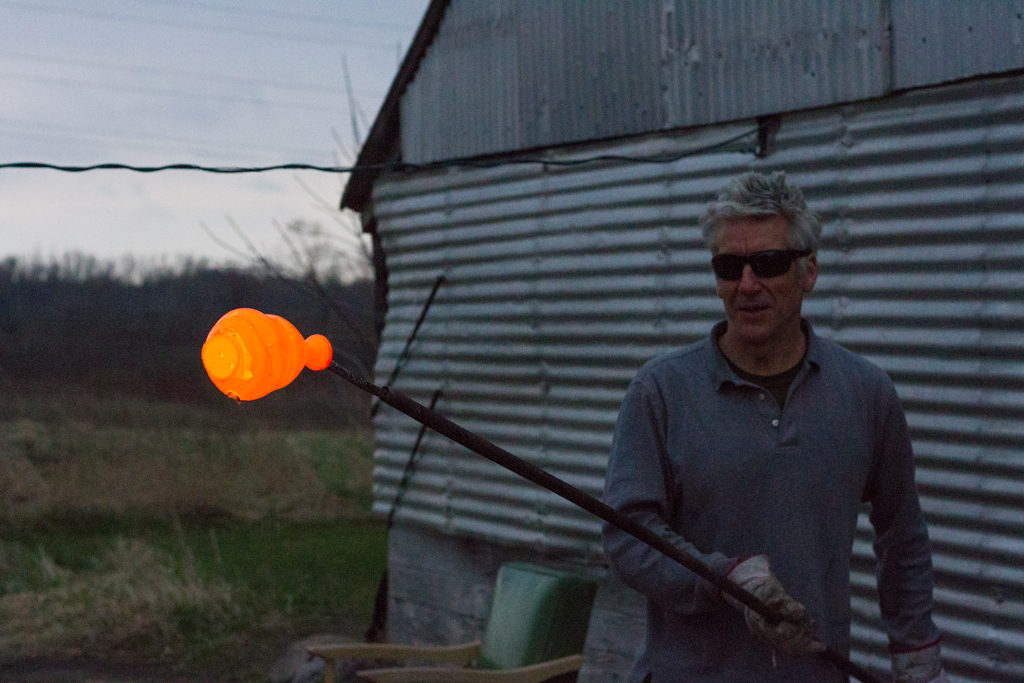
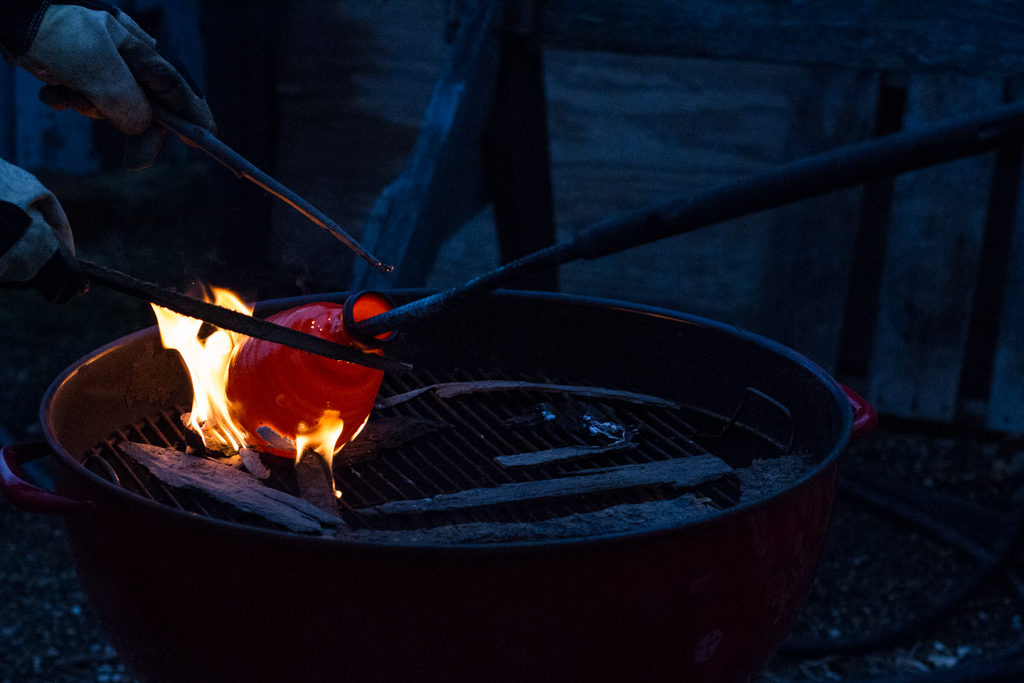

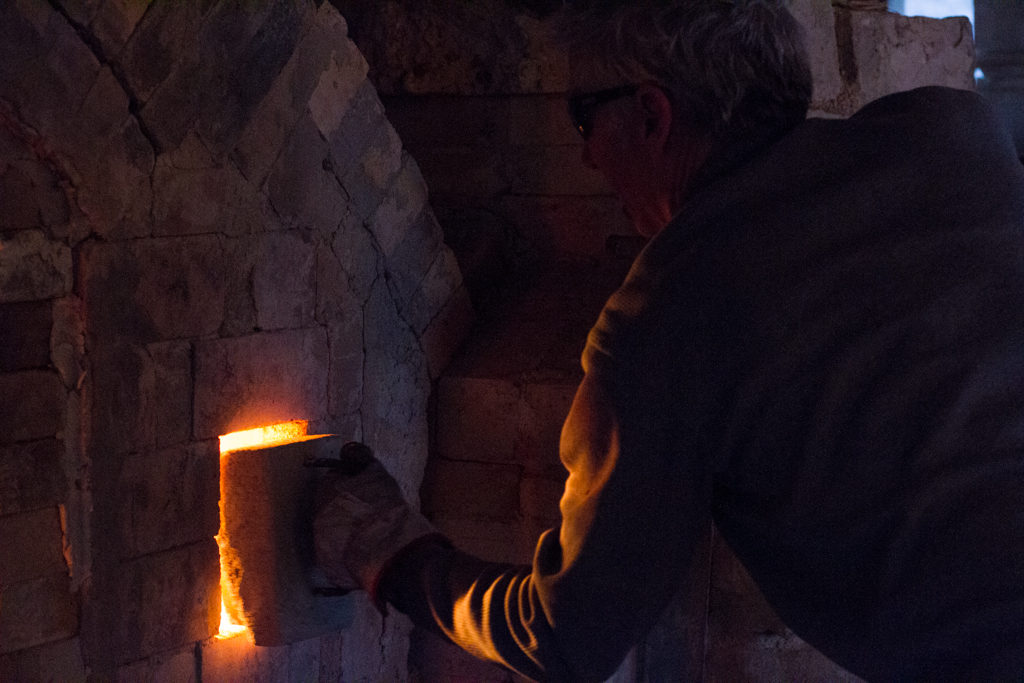
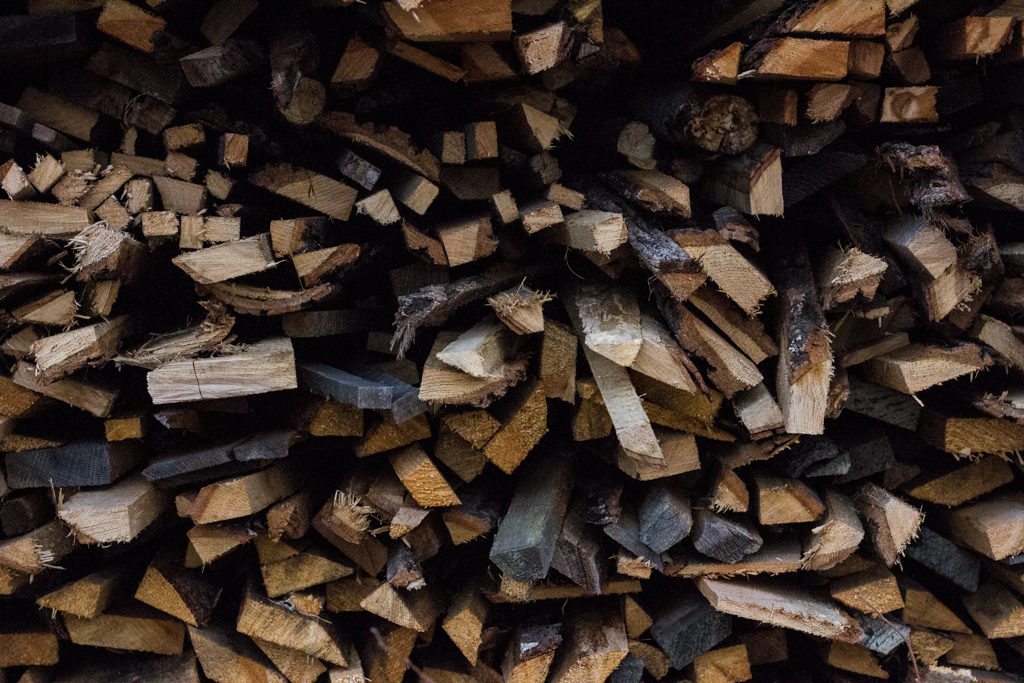